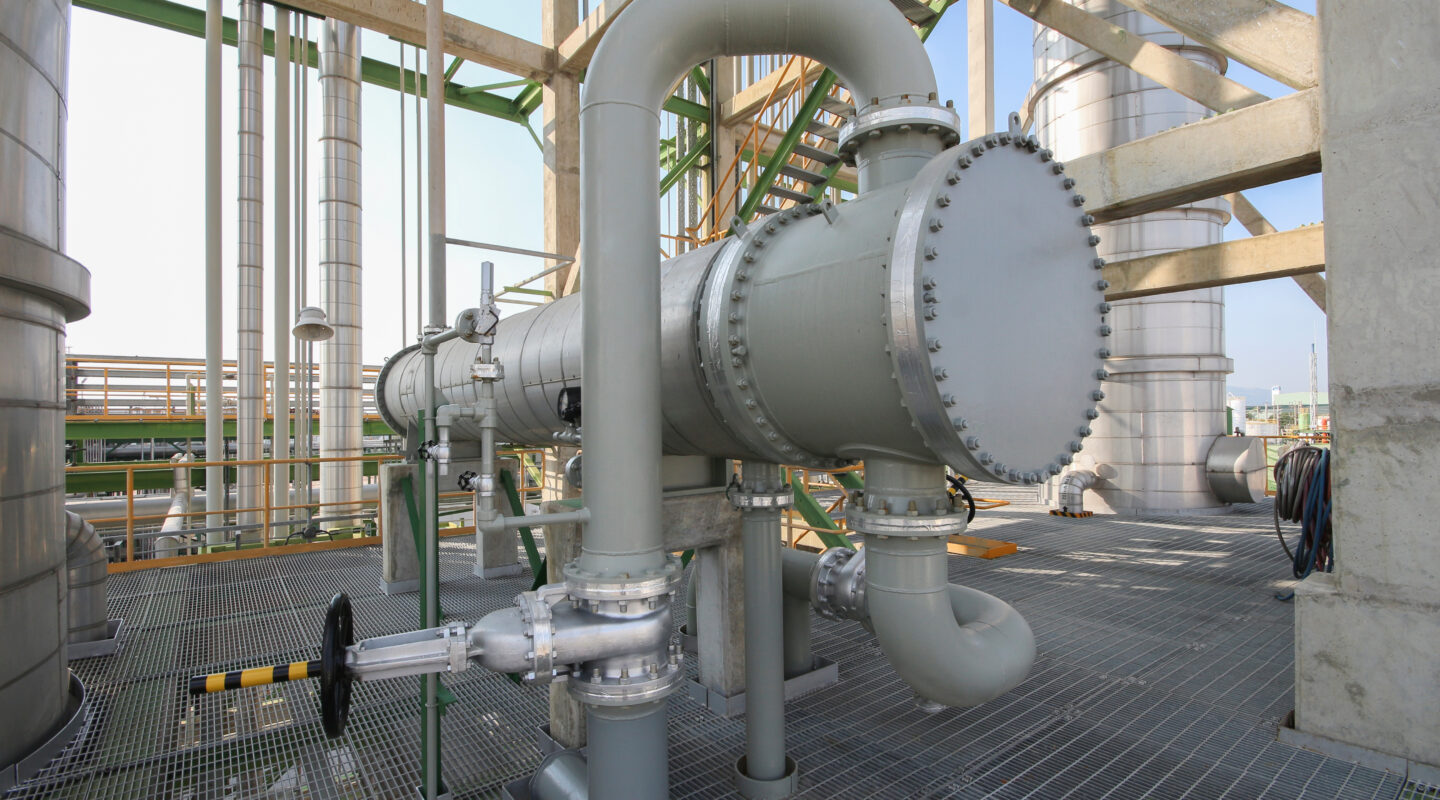
How NEON Sensors in Industrial Cooling Water Systems Enhance Efficiency and Safety
Background
This document aims to provide a comprehensive account of the challenges, solutions, and benefits associated with implementing a sophisticated temperature monitoring system in the Mild Hydrocracking (MHC) unit’s cooling water system (CWS) at the refinery of our customer, a major Oil & Gas company.
The CWS at the MHC unit of the refinery, a critical component in maintaining operational efficiency, began to show signs of strain under increasing demands. The system, originally designed to handle a certain capacity, struggled with the additional cooling water consumers introduced over time. The lack of adequate water pressure led to the gradual accumulation of residue, which resulted in increased clogging and occasional blockages.
These challenges ultimately compromised the efficiency and reliability of the cooling water system. This scenario was exacerbated by insufficient preparation and oversight in terms of water supply adaptation, leading to a system sensitive to heat load fluctuations and water quality variations.
The Challenge
Key challenges included:
Inadequate Water Supply and Distribution: The farthest and highest points in the CWS received water at lower flow rates and pressure, deviating from the design specifications. A 20% reduction in water flow rate at the most distant coolers
Increased Heat Load Issues: The inefficient operation of air coolers, followed by water coolers, led to a higher heat load, compounding the problem. Temperature imbalances lead to a 15% decrease in heat transfer efficiency.
Deposit Formation and Heat Transfer Inefficiency: Reduced flow velocity encouraged deposit formation, which impeded heat transfer and gradually decreased pipe cross-section, further reducing water flow.
These issues threatened to cause significant operational disruptions, including potential shutdowns for cleaning and, in severe cases, equipment replacement.
A historical trend showing a 10% year-on-year increase in maintenance and equipment replacement costs.
The Solution
In response, the refinery installed TWTG NEON temperature sensors at critical points of the D206 water cooler. These sensors were chosen for their precision and reliability. The data from these sensors was fed into the AVEVA OSIsoft PI system, creating a real-time monitoring dashboard. This setup enabled the Process Technologists and Unit Operations staff to have an unprecedented level of insight into the water-side conditions of the heat exchanger.
“By analyzing trends, the team could forecast potential issues, enabling proactive measures.”
Products Used
- NEON Temperature Sensors – (see datasheet at twtg.io)
Measurement – How It’s Done
The measurement process involved:
Continuous Data Collection: Temperature sensors provided ongoing data, capturing any anomalies in water temperature. Utilizing temperature data collected every 60 seconds from the sensors, with aggregated data (average, min. max.) every five minutes.
Advanced Data Analysis: Utilizing the SEEQ analytics tool, the team could compare actual performance against efficiency models, allowing for immediate identification of performance deviations.
Predictive Insights: By analyzing trends, the team could forecast potential issues, enabling proactive measures. Comparing real-time data against historical performance benchmarks. Analyzing temperature trends to predict potential efficiency drops.
Use Case Highlight
Incident Analysis and Continuous Monitoring at the refinery’s MHC Unit
In a notable incident on August 12, 2023, the HDS unit of the refinery experienced a process upset leading to a critical increase in water temperature. The TWTG NEON temperature sensors installed in the CWS immediately detected this anomaly, as the water temperature surged above 70°C, significantly higher than the operational norm. This sudden rise was critical, as the chemicals used for deposit prevention become less effective above 60°C, risking rapid deposit buildup and operational imbalances.
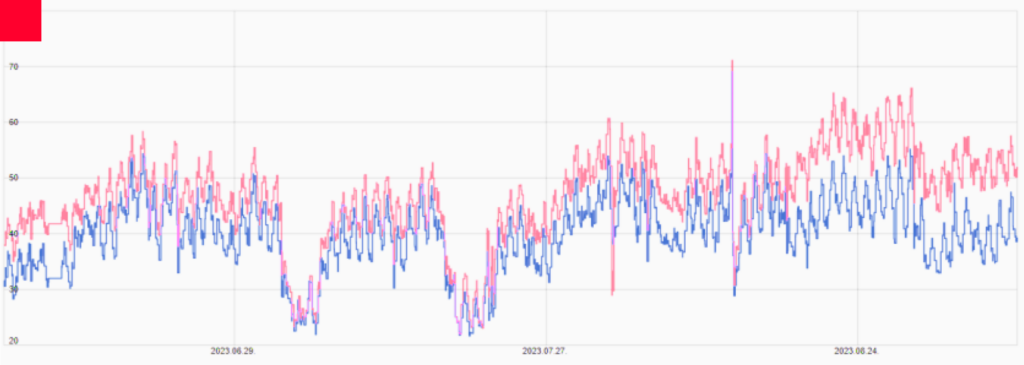
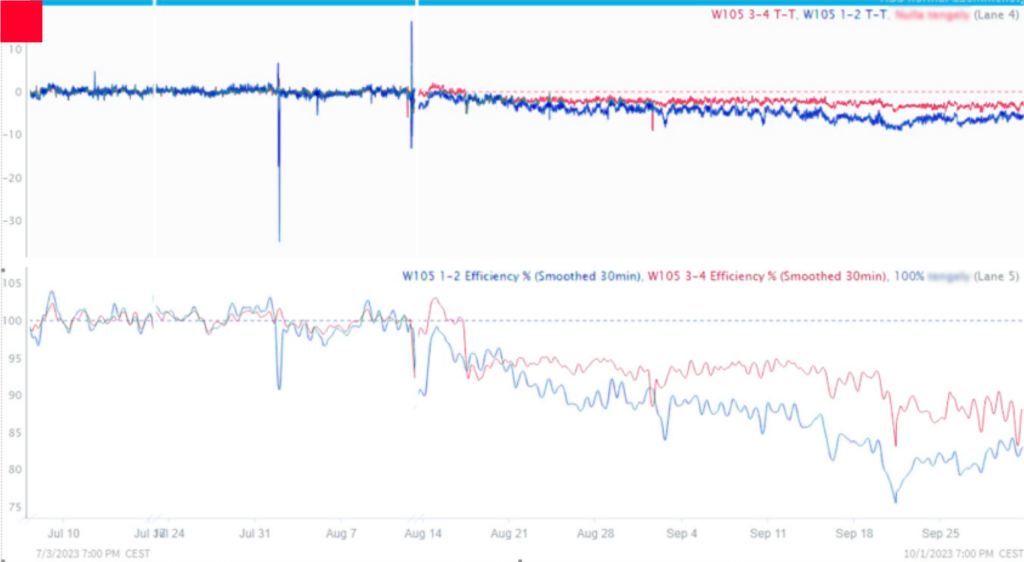
Using the data gathered and analyzed through the SEEQ tool, the Process Technologists and Unit Operations staff could clearly visualize the degradation in water cooler efficiency following the upset. The prompt identification of this issue enabled the team to undertake swift corrective actions, averting potential long-term damage and maintaining the system’s efficiency.
Beyond this specific incident, the continuous monitoring capability of the installed sensors has been instrumental in maintaining the overall health of the CWS. The ongoing data collection has allowed for real-time tracking of temperature fluctuations and performance trends. This constant vigilance has facilitated predictive maintenance, enabling the refinery to foresee and address potential issues before they escalate into major problems. As a result, there has been a marked reduction in unplanned maintenance activities, improved efficiency in heat
“Only 3 hours after receiving the business request, the team installed 4 TWTG NEON temperature sensors.”
transfer, and an extension in the lifespan of the cooling equipment.
Furthermore, the detailed temperature data and its analysis have not only proven invaluable in addressing immediate operational challenges but also in informing long-term strategic decisions. The insights gleaned from this data have guided decisions on equipment upgrades, process optimizations, and efficient resource allocation, leading to enhanced operational sustainability and efficiency.
This integration of advanced temperature monitoring and data analysis represents a significant stride in the refinery’s approach to operational management. It underscores the power of data-driven decision-making in optimizing industrial processes and highlights the refinery’s commitment to continuous improvement and innovation.
Conclusions
The implementation of this temperature monitoring solution marked a significant advancement in the refinery’s operational capabilities. It not only addressed the immediate challenges in the CWS but also set a new standard for system monitoring and management. The ability to detect and respond to issues promptly resulted in improved system reliability, reduced maintenance costs, and enhanced overall efficiency.
August 12, 2023, Incident: The sensors detected a 30°C spike in water temperature during a process upset, enabling rapid response. Post-incident analysis showed a potential 25% efficiency loss was averted.
Continuous Monitoring: Over six months, the system reported a 5% improvement in heat transfer efficiency and a 10% reduction in deposit formation.
Long-term Impact: Yearly analysis showed a 15% decrease in unplanned maintenance activities and a 20% reduction in associated costs.
Key benefits:
Real-Time Monitoring and Decision Making: Continuous temperature monitoring allowed for immediate detection and response to system inefficiencies.
Sustained Operational Efficiency: Constant performance tracking ensured that the cooling system operated within optimal parameters, maintaining high standards of production quality and efficiency. Achieved a 5% increase in overall efficiency.
Enhanced Safety and Reliability: The system’s improved reliability contributed to safer operational conditions, reducing the risk of equipment failure and associated hazards.
Data-Driven Operational Improvements: The insights gained from the temperature data analysis informed future improvements in the CWS, paving the way for more efficient and sustainable operations.
Cost-Effective Solutions: By preventing major shutdowns and equipment replacements, the solution proved to be cost-effective in the long run, ensuring the economic viability of the refinery’s operations. Achieved a 20% reduction in maintenance-related costs
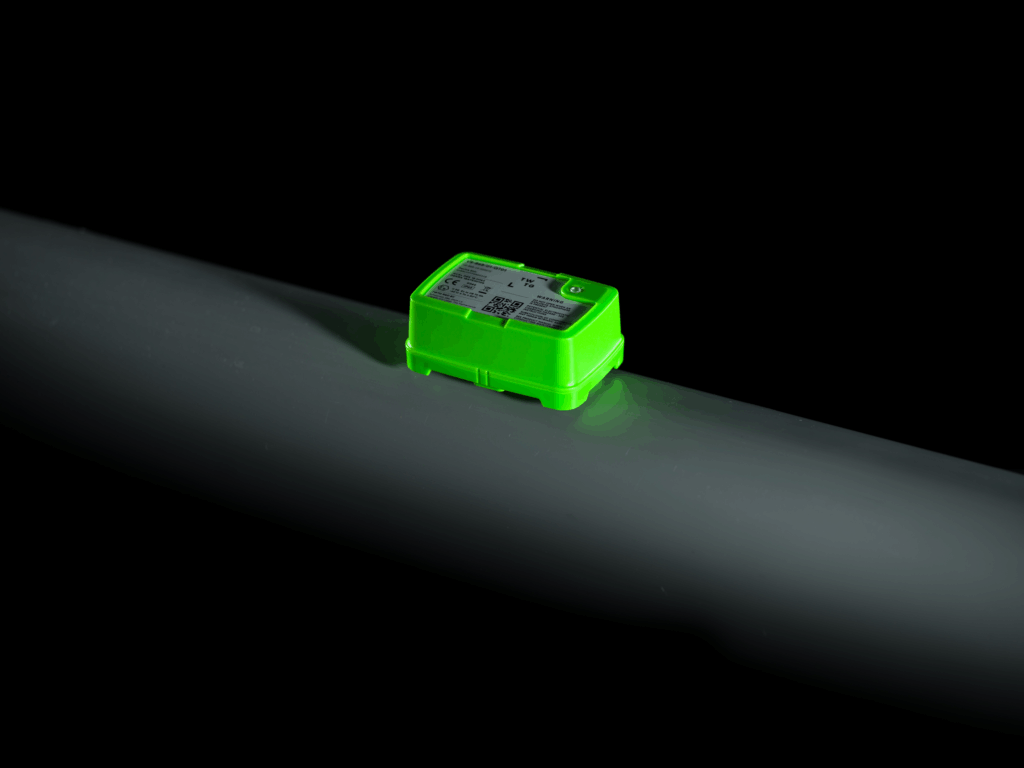