Harnessing the potential of the Industrial Internet of Things
On a misty morning, it is easy to say that every tank storage terminal looks much like any other. Cold concrete underfoot, storage tanks rising high into grey skies. But today under damp, heavy Rotterdam clouds, with drizzling rain not stopping at any point soon, there’s something different going on. Something special. Green boxes. Lots of them. Striking, against the dull mist and rain.
These boxes are actually Industrial Internet of Things (IoT) sensors, each attached to valves, pipelines, and storage tanks. These sensors make a passive object, such as a valve, smart. They provide knowledge and insight into a tank storage site. A real-time lens enabling customers a pioneering overview into this aspect of their operational process – all in one small green device.
Striking, against the dull mist and rain
Like its products, the inventors of these devices, TWTG stands out against the other solution providers in the oil and gas industry for its flexible and agile solutions.
The original founders, who are college friends, Dimer Schaefer and John Tillema entered the world of tank storage technology when they were approached by industry giant Vopak to develop some ground-breaking prototypes. These two industrial designers had always been driven to create something unique, with the raw ambition to create something that was the answer to a big question. A platform to showcase the creativity and innovation that would soon become the signature of TWTG.
At the time, Industrial IoT was in its nascency. Then, it was called machine-to-machine communication. For TWTG, though, product development was a good fit. It gave the young company an opportunity to prove its ability to a world-wide audience. A vision was born. Turning innate objects into smart solutions to provide insight and knowledge. Data to make informed decisions.
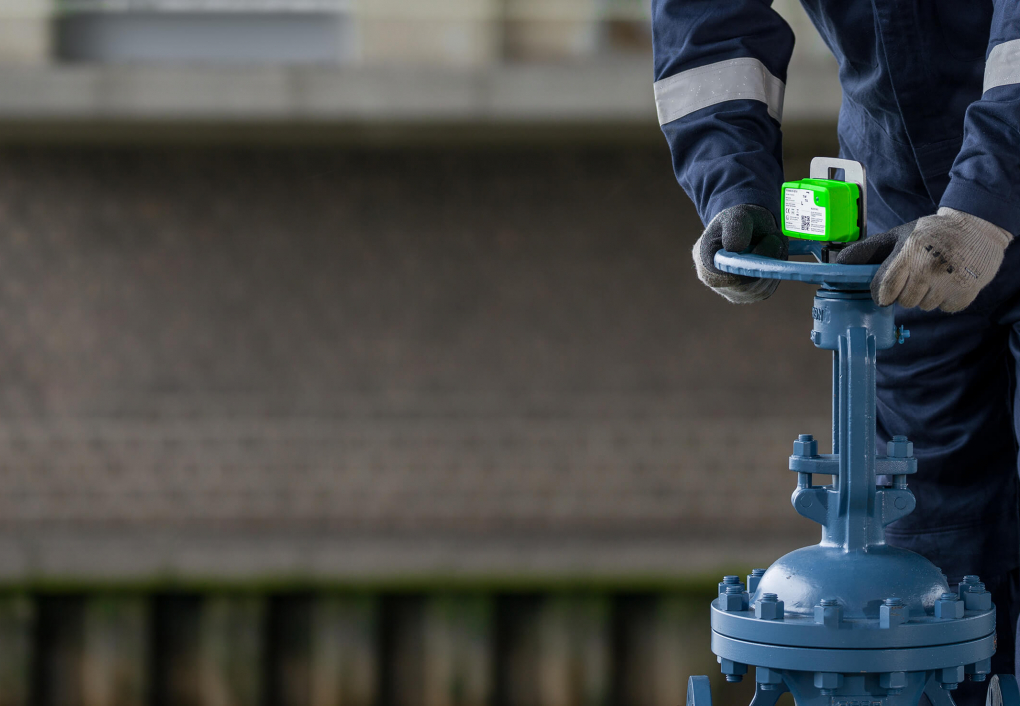
Sometimes, it is the combination of two or more things that make a real difference. A particular ingredient; a spark, that adds up to significantly more than the sum of its parts. A partnership. Tillema and Schaefer are a prime example of this. It is the counter-play of their very different strengths and abilities, which, when combined, create a very rounded point of view. The result is a balance and check that builds unbound confidence but at the same time – restraint. It provides not only flexibility but also stability.
Another unlikely combination of traditional engineering skill and technological capability is the growing relationship between heavy industry and IoT. Traditionally, with both large corporates and long-established organisations comes an inability to move quickly. Their uptake of new technology and solutions is notoriously glacial. The proverbial oil tankers trying to change course.

NEON Valve Sensor
Retrofittable I-IoT product that works on nearly all manually operated valves
View productBut here also, the world is changing. These organisations increasingly understand the benefits, in monetary and efficiency terms, of combining infrastructure and data to create insight. These companies are now looking more and more to employ or partner with visionaries. People who intuitively can conceive new applications for existing solutions. Companies with the ability to create a sum greater than the parts. It’s at this convergence that real innovation takes place, and where now, with the addition of a second letter ‘I’, the Industrial Internet of Things (I-IoT) was born.
And this is precisely why even in the midst of a grey and drizzly morning, the Vlaardingen site of Vopak looks different. Vopak is unique in its field. It has been able to create momentum, always keen to seek out improvement, eagerly exploring new opportunities and is continuously creative about finding new solutions to existing problems.
It is with this mindset, together with the recognition that not all problems can be addressed from within, that led Vopak to partner with TWTG. Unlikely partners – perhaps, but both parties benefit from this reciprocity. And their relationship is thriving.
IoT is the 4th industrial revolution. It is a topic that comes with some big expectations. But as with all revolutions, they can cause invested parties to be more than a little concerned. Change. Upheaval. Costs. The remarkably rapid advancement of recent technology has caught many industrial giants sleeping. Over the last decade, they have invested incredible sums of money into systems based on traditional working methodology. The truth is that this infrastructure is increasingly at risk of being labelled outdated. A couple of years back we were all aware of IoT and, to some degree, the potential of interconnecting our smart devices, but very few saw the magnitude of change that would come about.
The two great pillars of technology and engineering have begun to merge.

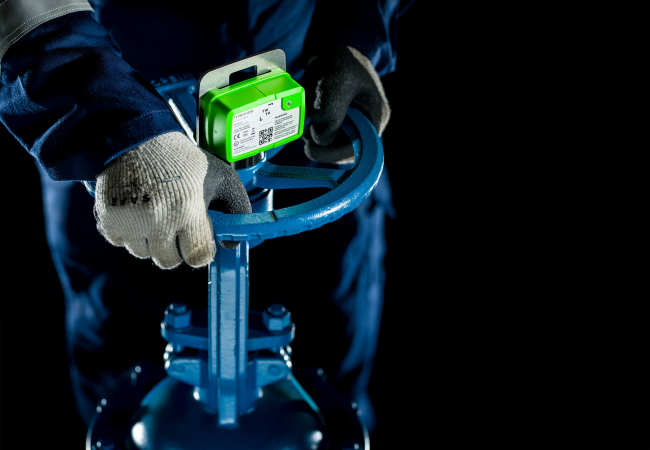
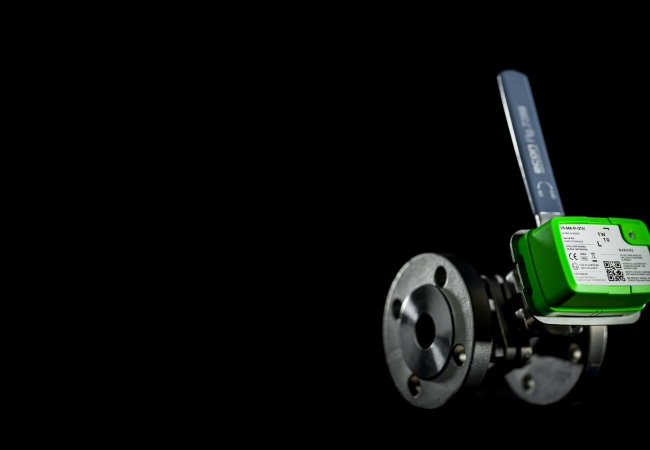

‘Digital twin’ is the new buzz word
The area in-between is where IoT firmly sits. In a short amount of time, we are starting to see engineers being just as likely to hold a tablet as a spanner.
So, while the ethos for many is revolution, the wise strategy for all is evolution. A gradual, planned approach to introduce new agile systems. Making the most of the infrastructure already in place and creating smart solutions that increase the functionality of this existing equipment.
Now, ‘digital twin’ is the new buzz word. It’s the goal on any strategists wish-list. This is when a company achieves the optimum set-up for infrastructure, where engineering and technology are perfectly integrated.
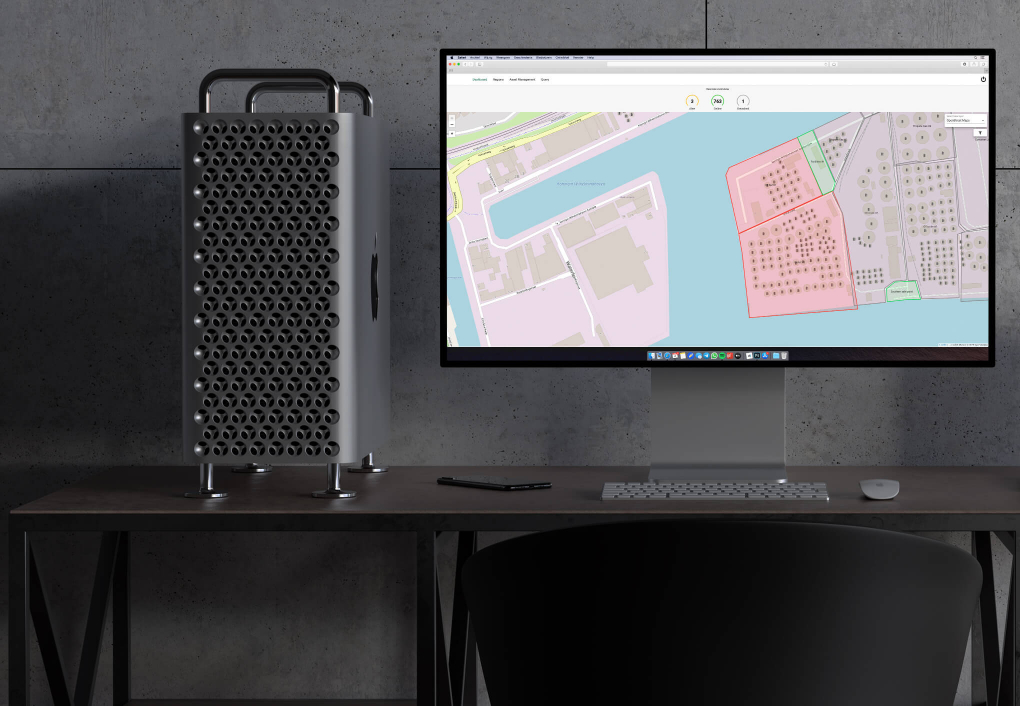
A holy-grail system that incorporates the perfect blend of IoT, machine learning, artificial intelligence, and data-analytics to create autonomous and semi-autonomous reactions to real-time influences and circumstance. A digital twin harvest, learns, and updates from system devices and infrastructure, from engineers, from sensors, and from external data sources that affect the decision-making process.
Environmentally and economically; the benefits of having a digital twin are obvious
The benefits of having a digital twin are obvious: Decision-making will be based on hard facts, figures, and pattern recognition, and as often the case, intervening before things go wrong. A correct decision made – maybe before a human realised the potential problem. So early a decision in fact, that the slightly uncomfortable truth is that most likely, the person never knew and never will.
This is an outstanding improvement to the previous situation where sites were solely reliant on individuals’ learned skills and experience, often necessitating lesser-trained people to perform critical tasks. With a perfect digital twin, operators could automatically receive alarms should components within a line-up not be configured to the necessary requirements. Personnel and autonomous equipment can be redirected in real-time to meet demands in other locations.
The possibilities of an extended IoT system are seemingly endless, and that is where the main problem lies. Where IoT starts, and where it ends. Where benefit is outweighed by the cost.
Evolution is needed
So, to balance a desire to maintain existing sites and infrastructure, but where possible, to create new insight and knowledge to improve decision-making, we see ourselves with a need to develop new solutions. And by far, the best solution is based on retrofitting smart devices onto already existing equipment.
Environmentally and economically, the simple replacement of a component should not and cannot be the first answer in an industrial scenario. Here costs have been tied up, and capital investment carefully considered, so it is good for the old system architects and new accountants that in reality, wholesale change is usually unnecessary. Hence, evolution is needed.
It has been shown time and again that partnerships work
TWTG & Vopak
It has been shown time and again that partnerships work. Whether it is the combination of the engineering and technology sectors, Vopak and TWTG, Schaefer and Tillema, or merely a smart device and its data. Partnerships deliver more than the sum of their parts.
So, if partnerships lead the way to create innovative new solutions, then choosing the right partners is key to whether these solutions can be successful or not. Companies need to select wisely to with whom they partner. A partnership should be a symbiotic relationship.
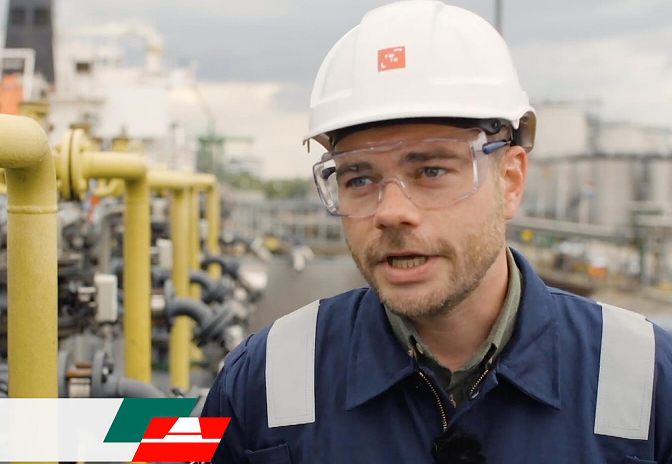
To fit into a corporate’s wider eco-system, players’ abilities need to complement each other, to increase both their potential and capability, while achieving both their mutual and individual ambitions.
If industrial organisations want to move forward, they have to plan effectively for the future. This may sound obvious, but really the one known fact is that their future is now fluid. Industries are changing fast. Energy sources are starting to shift away from traditional fuels. Increasingly competitive markets always push margins. The next technological advances of tomorrow mean that companies have to plan to be both agile and flexible. To bend to the market, and crucially stay focused on its shifting sands.
Flexibility is the key, investing in systems that are developed with change in mind. A mindset to experiment with new solutions to better understand capabilities and potential. Companies need to act more entrepreneurially, creating interoperability and therefore commiting to outcome and not to contractual longevity.
This flexibility is the objective for a new era of industrial system designers. No longer are companies willing to pin their futures on closed system – they want options, integrations, longlasting improvements. Neither are they willing to offer exclusivity to individual systems integrators who traditionally end up the kingmaker in any future integration plans. Companies want choice. They want the best partner possible to provide unique solutions. Forward thinking partners. Partners that add value.
And this is the case between Vopak and TWTG, where an exciting and expert scale-up company provides the ways of thinking and fast solution development that a corporate has trouble creating internally and where one of the oldest organisations in The Netherlands can provide the market knowledge and operational experience that a young company cannot replicate and hence learn from.
This technical feature was written for TankStorage Magazine. A PDF-version can be found here.