TotalEnergies is one of the leading oil and gas companies in the world. With 25 refineries running 24/7 across the globe, it is essential to have a complete overview of the current operational status of all their assets to maintain an efficient and safe environment. One of the challenges is to manage the thousands of items of rotating equipment installed on each site. These assets vary from pumps, gearboxes and fans, to static equipment with resonance issues.
Historically, assets are monitored at intervals, often monthly with manual vibration measurement to verify an asset is correctly functioning and possibly detect a failure early.
During this snapshot, vibrations are measured over a broad spectrum and then analysed by an expert to determine whether further action is needed. While this process helps to manage unexpected downtime, it has a number of significant downsides:
- It is extremely labour intensive.
- Substantial gaps between snapshots may not catch all potential issues in time, risking possible catastrophic failure taking place in between the checks carried out.
Total Refinery Antwerp has tested TWTG’s NEON Vibration Sensors to address and improve on the typical downsides of vibration measurement.
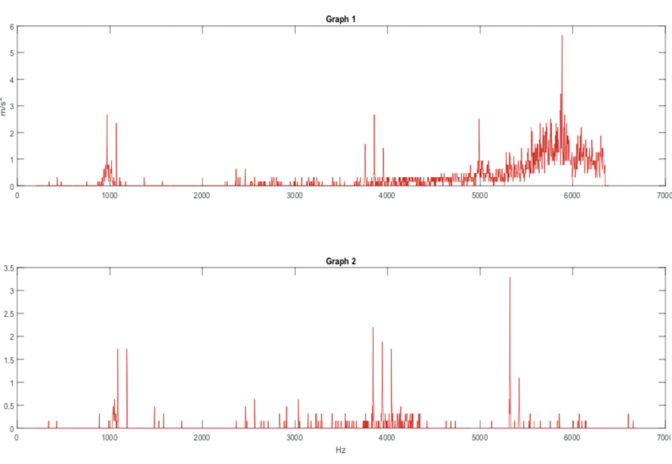
TWTG’s NEON Vibration Sensor gives us better use of our time. We don’t need to go out when the sensor indicates all levels are OK; Spending time only on the assets with actual problems.
Franky Oste, TotalEnergies Reliability Engineer
TotalEnergies Use-Case
The NEON Vibration Sensor was installed on the bearing housing of the pump block within a pump installation. This device sends an RMS velocity value at 15-minute intervals, which creates excellent insight into the overall condition of the asset and, as such, is a significant upgrade from monthly monitoring.
In addition to the single value, the sensor also transmits every two days (which is only advisable for short periods in these maintenance use cases) a full FFT measurement for deeper analytics. This full-spectrum, unfiltered measurement allowed TotalEnergies to benefit from a complete view of the ongoing status of assets in the field and resulted in detailed information.
Soon after installation within the TotalEnergies Refinery, there was a change in the usual behaviour recorded so far, with a distinct drop in vibration levels. The evaluation of the data from the RMS velocity and acceleration, combined with the detailed information from the FFT has now been recognised as an early warning signal and therefore been integrated into the day to day maintenance routine for TotalEnergies Antwerp.
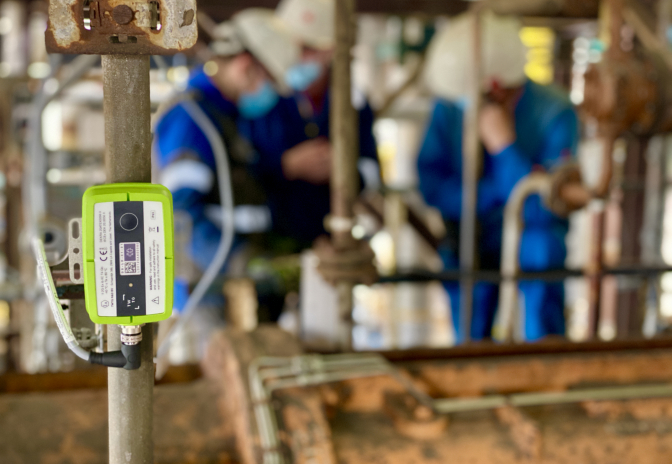
Comparing graphs 1 and 2, we see three apparent changes between the two graphs. The first clear difference in the FFT is a decreased amplitude at around 1100 Hz. Next, the second indicator displays the same behaviour but at a higher frequency. Finally, the last and most significant difference is seen in a big bump, a so-called ‘Haystack’ in the spectrum between 6000 and 6666 HZ.
The NEON expanded frequency range vs. competitors made this visible. After comparing these two measurements, it was apparent something unusual was happening. Upon closer inspection, engineers realised this lower level of acceleration was occurring immediately after relubrication. Measuring low levels of acceleration would indicate correct lubrication to have taken place. What was however seen was the sharp drop of vibration levels, followed by a quick rise of the vibration data collected, pointing to ‘over lubrication’, which could cause long-term machinery damage.
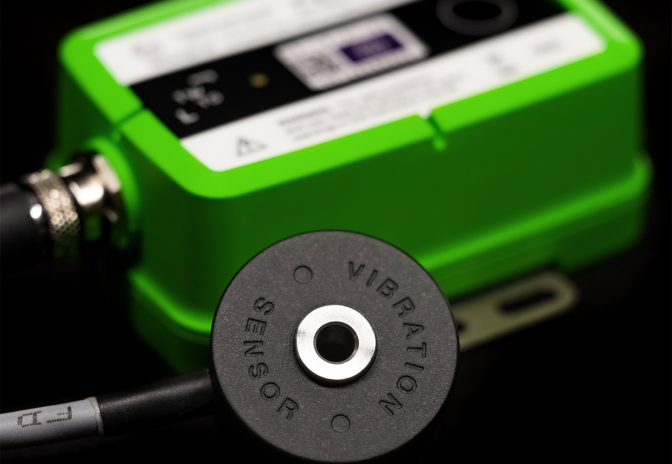