Background
In the oil and gas industry, maintaining optimal cooling efficiency is essential for ensuring operational reliability, equipment longevity, and plant safety. Cooling systems, such as belt-driven fin fans, play a crucial role in regulating process temperatures and preventing overheating, which can lead to costly downtime or equipment failure.
One of our customers, a major energy and chemicals company, operates multiple belt-driven fin fans to cool process liquids in their refinery. To monitor these critical assets, their engineers typically conduct manual vibration measurements to assess fan health and detect potential mechanical issues. However, this approach has several limitations—it is sporadic, time- consuming, and dependent on scheduled inspections, which may not catch early-stage faults before they escalate into significant failures. Additionally, manual monitoring poses safety risks for engineers working in high-temperature or hard-to-access environments.
To improve efficiency, the customer sought an advanced, automated monitoring solution. This use case illustrates the significant benefits of implementing a near real-time vibration monitoring system, which provides continuous insights into equipment performance, detects early warning signs of potential issues and improves plant safety in hazardous environments.
The Challenge
Belt-driven fin fans rely on motor-driven pulleys and belts to function correctly. As belts degrade over time, their grip on the motor-driven pulleys weakens, reducing the fan’s rotational speed and overall efficiency. Slippage can occur gradually and unpredictably, and by the time it is detected, the damage is often already done.
For a refinery, this can be particularly challenging and costly:
• Unplanned Downtime: If the cooling system fails, production may need to be halted, leading to lost productivity and revenue.
• Increased Maintenance Costs: Frequent belt replacements, repairs, and potential motor damage can drive up maintenance expenses.
• Reduced Cooling Efficiency: Overheating of machine equipment can increase the risk of operational failure.
• Higher Energy Consumption: Slipping belts cause inefficiencies, forcing motors to work harder and consume more electricity.
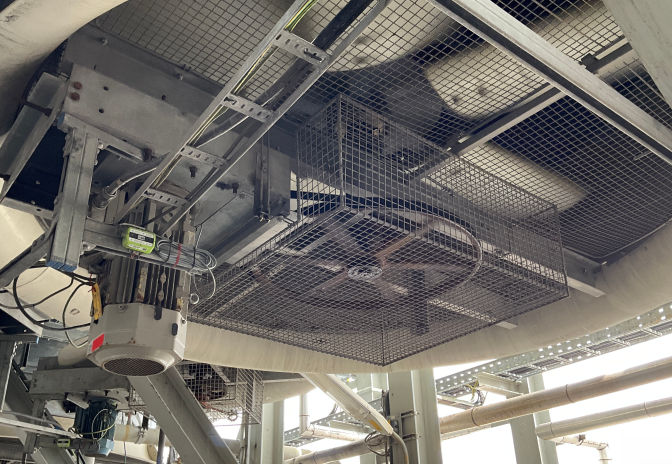
The Solution
In order to mitigate these issues, the refinery implemented NEON Vibration Sensors, integrated with SolidRed, for near real-time data visualisation. The sensors were installed directly on the motors driving the fin fans, enabling precise measurement of vibration levels.
With automated monitoring, the sensors continuously track vibration levels, identifying anomalies before they become critical. If vibrations exceed a predefined threshold, the system immediately triggers an alert, allowing engineers to intervene before the issue escalates.
Beyond simple detection, our sensors offer precision analysis, excelling at measuring low-frequency and ‘sub-synchronous’ vibrations—those occurring at frequencies lower than the fan’s operating speed. These subtle vibrations can indicate mechanical issues such as misalignment or looseness, helping engineers diagnose potential failures early.
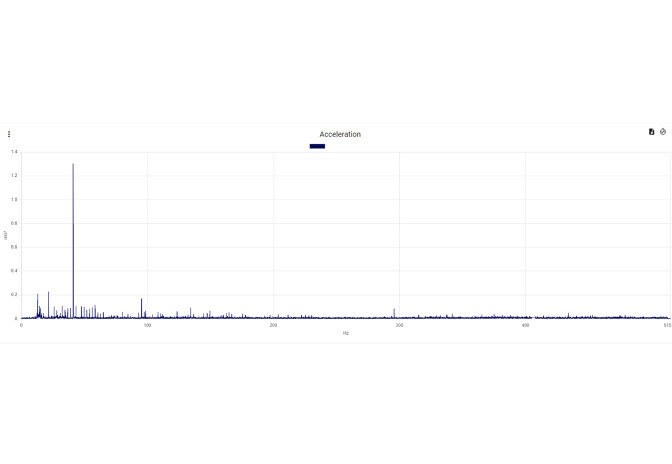
With SolidRed, engineers can remotely access near real-time data, minimising the need for on-site inspections and improving plant safety.
A smarter, proactive way to spot slippage early, before it causes failures.
Products Used
- NEON Vibration Sensor – (see datasheet at twtg.io)
- SolidRed Software Suite – (see datasheet at twtg.io)
Key Benefits
The NEON Vibration Sensors and SolidRed software have become an integral part of our customer’s maintenance strategy. A solution that has the potential to lead to a significant 35% reduction in unplanned downtime, a 25% increase in machinery lifespan, and a 20% decrease in maintenance costs.
Since implementation, the refinery has benefited from:
• Predictive Maintenance Efficiency – Engineers now receive alerts before failures occur, allowing for timely interventions.
• Reduced Downtime & Costs – By replacing belts before they fail, the customer minimises costly repairs and operational disruptions.
• Improved Safety – Reduced need for manual inspections in hazardous environments.
• Scalability – Following the success of the initial deployment, the customer plans to expand the solution across multiple business units
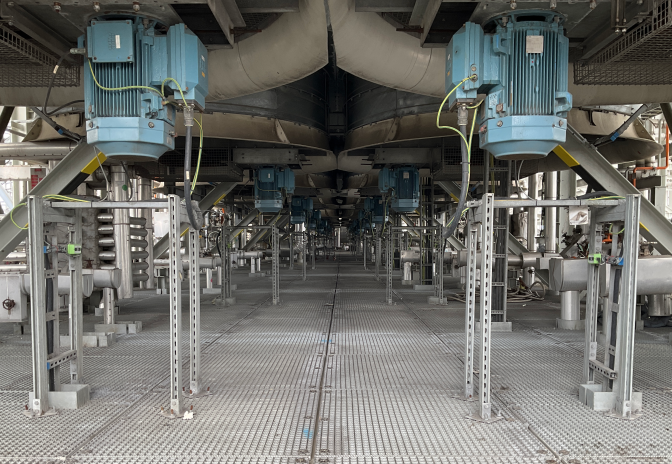
Conclusions
This use case demonstrates how transitioning from manual inspections to an automated, sensor-based monitoring system has improved operational efficiency, enhanced safety, and reduced costs for our customer. TWTG’s NEON Vibration Sensors and SolidRed software ensure the refinery’s fin fan system now operates at peak performance.
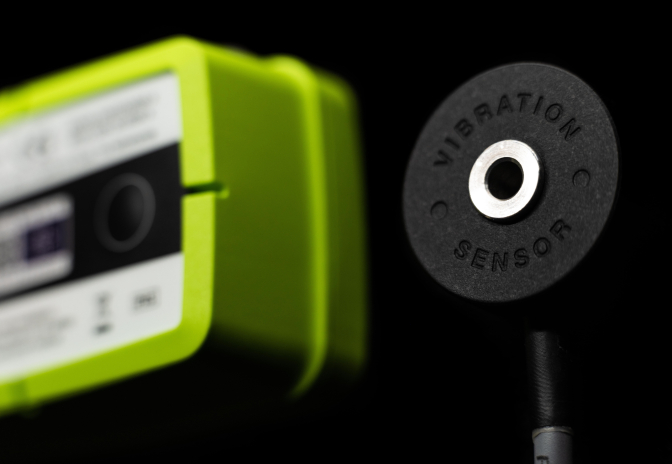
Initially implemented in one business unit, the solution’s success has led the refinery to expand its use across additional units. As a result, over 400 sensors are now in operation, becoming a standard part of our customer’s maintenance strategy.